Haili Group, one of the largest robotic factories in Shanghai, currently owns 480 industrial robots. Since 2007, it has replaced 357 first-line jobs, equivalent to nearly 1,000 first-line workers. After 9 years of recruiting the first robot, Haili Group tasted a lot of sweetness: In 2015, the cost of using a robot was less than 60,000 yuan/year, and the cost of using a worker was nearly 100,000 yuan/year. Haili Group, which produces air-conditioning "hearts" - compressors, has one of the largest robot factories in Shanghai. In the view of Highly, the compressor manufacturing industry can still be retained on the banks of the Huangpu River, where the cost is high. Because "recruiting" robotic employees, Haili won a strategic space. In fact, in addition to the industrial robots used in manufacturing, intelligent robots also replace the artificial ones, and more and more people play the role of customer service in the financial and other fields. CCB and China Merchants Bank have thus saved a total of 9,000 manual customer service. "Science Fiction" workshop: 3 workers + 8 robots "Iron arm" is everywhere, workers are scattered. Flip, swing, grab, put down... At a high temperature of 600 degrees Celsius, the Bumblebee's color robot "arm" moves freely, as long as 10 seconds, three or four pounds of silver-white metal coil from take to put to the next Work station, the process can be called "fast and accurate." After a pipeline process, the end of the line was filled with a molded compressor "coat" shell. Each robot here is in a fixed position and can operate two or more devices. 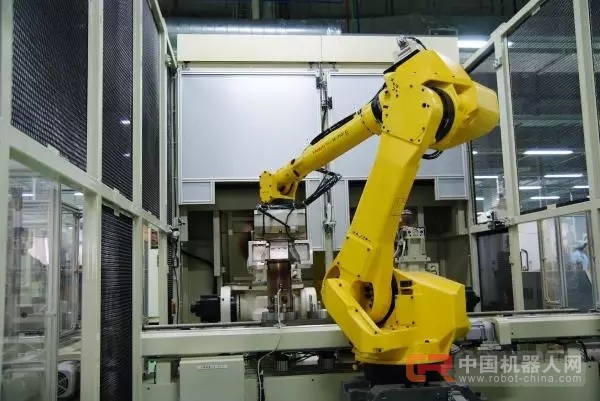
Haili Group's human and machine "dancing together": Robots resolve labor cost pressure This is not a scene in science fiction movies, but a real scene of the Shanghai factory's sheet metal workshop. In the plasma welding station, several workers spread their lives. Their role is either “supervisor†or “doctorâ€. The regulation and control of robotic equipment and sample testing products are done by workers. As early as before the robot "into service", this compressor shell production line required about 15 workers to complete production tasks. Since 2007, after the "recruiting" of robots, the current staffing structure has become: 3 workers + 8 units. robot. The compressor is the heart of air conditioners and refrigerators. The task of the sheet metal workshop is to process the steel sheet into a compressor shell. At present, there are 22 robots in this workshop, and the number of workers has been reduced from 144 in 2007 to 20, which means that once the work of 124 workers has been performed by robots, the workers “reduction†86%. . In addition to sheet metal, the rest of the "arm-arm partners" are carrying, bundling, and even screwing in the assembly process. Up to now, the entire Highly Group has owned 480 industrial robots. Since 2007, it has replaced 357 first-line jobs, equivalent to nearly 1,000 first-line workers. Two costs: The robot price is reduced by 5% per year. The labor cost is increased by 10%. The compressor industry is a labor-intensive industry, and much of the work is done manually. However, with the gradual disappearance of the demographic dividend, the problem of “recruitment difficulties and labor shortage†has emerged several years ago. In the Shanghai factory of Highly Group, the labor cost accounts for 47% of the total manufacturing cost. In order to cope with the increase in labor costs, Highly stepped out of Shanghai in 2007 and set up new branches in Nanchang and Mianyang. India's manufacturing base has also been built. At present, Shanghai bases account for less than 60% of the Group's total production capacity. “Our manufacturing companies like this need to hire a large number of laborers. After nearly a year of long holidays such as the Spring Festival, some employees in the front line are losing. Some of the post-1980s are reluctant to carry out heavy-duty operations on the production line.†Zheng Min, general manager of the company, told the reporter: “The peak of departure from February to March is exactly the peak of our production period. The average turnover rate of 33% will interfere with normal production. At the same time, the frequent replacement of frontline workers will affect product quality and increase equipment damage rate. And safety hidden troubles.†Of course, when recruiting the first robot in 2007, the Haili Group was not without hesitation: Taking the Shanghai factory as an example, the labor cost of the first-line workers was about 37,000 yuan per year, and the robot calculated the depreciation. The annual cost is 73,000 yuan, almost doubled. However, at the same time, labor costs have increased at a rate of about 10% per year, while robot prices have fallen by about 5% per year. Chairman Shen Jianfang, the then general manager, pondered Hai Li's sustainable development, established the strategic vision of "the world's first air-conditioning compressor supplier", proposed the next step in competition with multinational companies, and must further develop technical capabilities and manufacturing capabilities. Innovation and improvement. The transformation and upgrading of enterprises requires not only the development of new products, but also the level of intelligence in production systems. Thus, we saw the "fast run" of the later Highly Applied Robot. In fact, by 2011, the cost of using a robot is already lower than that of using a worker. The Shanghai factory is still used as an example. The former costs 63,000 yuan each year, while the latter requires 67,000 yuan. Moreover, this group of "scissors" is still expanding. By 2014, the advantages of robots have become more apparent. This set of figures has become 56,000 yuan and 92,000 yuan. "Recruiting" robotic employees has secured strategic space for Highly. In Highly view, even in the cost of the Huangpu River, the compressor manufacturing industry can still be retained. "HR Part 2": Keeping track of the robot's archives How does the number of Haili's robots have reached? In mid-2015, IFR (International Federation of Robotics) counts the density of industrial robots in various countries of the world, with the highest number of 437 Taiwan/10,000 industrial workers, followed by Japan with 323 Taiwan/10,000 industrial workers, and the third with 282 units/ten thousand Germans. Industrial workers, while the world average of 66 Taiwan / ten thousand industrial workers, China only 36 Taiwan / ten thousand industrial workers, below the world average. Zheng Min stated that at present, the Shanghai factory has reached 569 sets/ten thousand industrial workers, and has surpassed the highest South Korea, and is at the world's leading level. In order to manage these robots well, the Shanghai factory has a “second human resources departmentâ€: the production technology department assumes the human resources management of the robots. More than 230 robots have invested a total of 187 million yuan in 2007, 288 jobs have been reduced, and 861 people ... Chen Jielu, chief of the automation promotion department, said that the production technology department will number each robot to keep track of the robot's return on investment. At present, one machine passes three shifts of working time, which is equivalent to the output of three production employees. According to the 2015 automation project calculation, the average investment return period is 3 years. On the other hand, the “second human resources department†is responsible for the “turning work†of the robot according to the adjustment of the work station, which can be easily realized by changing the manipulator configuration of the robot, reducing the difficulty of personnel transfer and labor costs, and has high versatility. The labor cost saved by the robot can also realize internal reinvestment. For example, after three years of depreciation to recover the investment, the labor cost saved by the robot continues to work and a pool of funds is formed to achieve self-recycling through reinvestment. Increased production capacity: The per capita production capacity increased from 295 to 1,131 units. Without robots, staff instability can cause production fluctuations. For example, departures and training of newcomers make staff operations fluctuate drastically, and human factors such as fatigue, worker's mood, and skill proficiency may also cause uncertainty. After the robots “go on dutyâ€, they can maintain a stable and efficient working status for a long period of time, achieve low production fluctuations, improve on-time delivery rates, reduce work-in-process inventory, and comprehensively improve on-site management. Compared with the efficiency of the robot, the efficiency of the robot is different at different time periods within a shift: the efficiency of the personnel is up to 90%, and the minimum is 0%. It will fluctuate at any time, and the efficiency of the robot will be stable at around 90%. Take the Shanghai factory sheet metal shell production line as an example. Before using the robot, there were 10 operators per class, with a production capacity of 2949 compressors, a per capita capacity of 295 units, and a per capita operating equipment of 1.2 units; after using robots, each class was reduced to 3 people. However, the production capacity was expanded to 3,392 units, with a per capita capacity of 1,131 units and 7.7 units of operating equipment per capita. Man-machine "dancing together": Workers' transformation is an inevitable move. Robots do not mean that workers are laid off. "In the year since the introduction of robots in 2007, there has been no centralized large-scale resignation." Zheng Min told reporters that there was a definite turnover rate for the first-line laborers. In addition to reducing recruitment, the replacement of nearly 1,000 workers by robots is a gradual decline. After the robot came, the "workers" who danced with it were also beneficiaries. “In 2005, we organized the Haili College of Power and jointly operated with the University of Television Broadcasting to allow workers to read college classes and undergraduate classes.†Zheng Min introduced that after training, some workers were liberated from the original heavy physical position and they are now on the spot. The work of the workers mainly focuses on equipment maintenance and product testing, and they are transformed into robot managers. Labor intensity declines and incomes increase substantially. The increase in income is the most visible "benefit." Highly use of robots in Highly, the increase in employee labor efficiency, the increase in employee income. Last year, the per capita annual cash income of the Shanghai factory sheet metal workshop rose from 37,000 yuan in 2007 to 84,000 yuan. In terms of improving occupational health, robots can replace artificial hands in harsh environments such as noise and high temperatures. According to reports, high-speed rushing station noise reaches 97 decibels, electric sawing saws wood sounds at 90 decibels, and exposure to noise from 70 decibels to 90 decibels for five years, the risk of hypertension is as high as 2.47 times. Workers who were originally engaged in high repetitiveness and labor intensity can work on jobs with higher skill requirements and lower labor intensity, which strengthens the company's ability to innovate and are more conducive to the realization of employees' personal values. It can be said that the use of robots is a win-win thing for both companies and employees. Highly Meaning: Robots Resolve Manpower Cost Pressures To upgrade and upgrade a company, it is not only necessary to develop new products, but also to require intelligent and flexible production. In the face of disappearing demographic dividends and high labor costs, the exploration of Haley's applied robots has sample significance for other companies. At present, the Highly Group has taken the lead in completing the international industrial layout in the industry. It has five world-class compressor plants and seven technical centers worldwide. Its products are sold in more than 160 countries and regions, and there are one for every seven air conditioners in the world. Hasli compressor is used. As a traditional household appliance manufacturing company, Highly was able to take the lead in realizing the internationalization of its industrial layout. One of the factors that has long dominated the world's top three market share is the introduction of intelligent automated production models and the introduction of robot “employees.†As robots can effectively resolve the pressure of rising labor costs and protect the advantages of domestic manufacturing companies in other areas, Zheng Min believes that China's status as a “world factory†will not be easily replaced. The world’s industrial robots have long been the most used in the automotive industry, working on welding, stamping and painting. But now, robots are "big attacks" in various industries, from the handling of valuables such as tobacco and Wuliangye, to the brick making, food and beverage industries, and even the feed industry. In fact, more and more labor-intensive companies in China have also begun to try robots. Zheng Min believes that Highly's robot application model is fully conditional in other batch, standardized, and process-oriented manufacturing industries. Highly is currently preparing a robot plan for 2020. In the future, most of the workshops in Shanghai are expected to be fully automated.
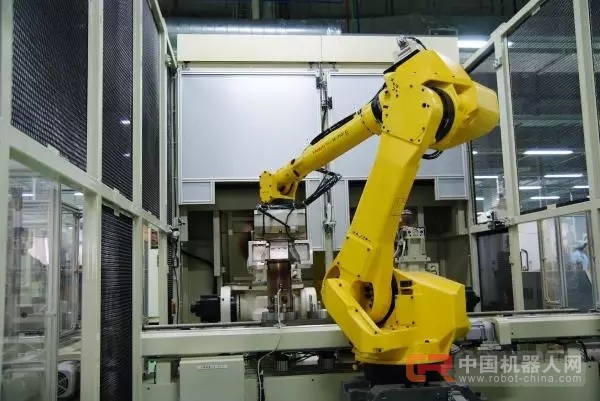
Haili Group's human and machine "dancing together": Robots resolve labor cost pressure This is not a scene in science fiction movies, but a real scene of the Shanghai factory's sheet metal workshop. In the plasma welding station, several workers spread their lives. Their role is either “supervisor†or “doctorâ€. The regulation and control of robotic equipment and sample testing products are done by workers. As early as before the robot "into service", this compressor shell production line required about 15 workers to complete production tasks. Since 2007, after the "recruiting" of robots, the current staffing structure has become: 3 workers + 8 units. robot. The compressor is the heart of air conditioners and refrigerators. The task of the sheet metal workshop is to process the steel sheet into a compressor shell. At present, there are 22 robots in this workshop, and the number of workers has been reduced from 144 in 2007 to 20, which means that once the work of 124 workers has been performed by robots, the workers “reduction†86%. . In addition to sheet metal, the rest of the "arm-arm partners" are carrying, bundling, and even screwing in the assembly process. Up to now, the entire Highly Group has owned 480 industrial robots. Since 2007, it has replaced 357 first-line jobs, equivalent to nearly 1,000 first-line workers. Two costs: The robot price is reduced by 5% per year. The labor cost is increased by 10%. The compressor industry is a labor-intensive industry, and much of the work is done manually. However, with the gradual disappearance of the demographic dividend, the problem of “recruitment difficulties and labor shortage†has emerged several years ago. In the Shanghai factory of Highly Group, the labor cost accounts for 47% of the total manufacturing cost. In order to cope with the increase in labor costs, Highly stepped out of Shanghai in 2007 and set up new branches in Nanchang and Mianyang. India's manufacturing base has also been built. At present, Shanghai bases account for less than 60% of the Group's total production capacity. “Our manufacturing companies like this need to hire a large number of laborers. After nearly a year of long holidays such as the Spring Festival, some employees in the front line are losing. Some of the post-1980s are reluctant to carry out heavy-duty operations on the production line.†Zheng Min, general manager of the company, told the reporter: “The peak of departure from February to March is exactly the peak of our production period. The average turnover rate of 33% will interfere with normal production. At the same time, the frequent replacement of frontline workers will affect product quality and increase equipment damage rate. And safety hidden troubles.†Of course, when recruiting the first robot in 2007, the Haili Group was not without hesitation: Taking the Shanghai factory as an example, the labor cost of the first-line workers was about 37,000 yuan per year, and the robot calculated the depreciation. The annual cost is 73,000 yuan, almost doubled. However, at the same time, labor costs have increased at a rate of about 10% per year, while robot prices have fallen by about 5% per year. Chairman Shen Jianfang, the then general manager, pondered Hai Li's sustainable development, established the strategic vision of "the world's first air-conditioning compressor supplier", proposed the next step in competition with multinational companies, and must further develop technical capabilities and manufacturing capabilities. Innovation and improvement. The transformation and upgrading of enterprises requires not only the development of new products, but also the level of intelligence in production systems. Thus, we saw the "fast run" of the later Highly Applied Robot. In fact, by 2011, the cost of using a robot is already lower than that of using a worker. The Shanghai factory is still used as an example. The former costs 63,000 yuan each year, while the latter requires 67,000 yuan. Moreover, this group of "scissors" is still expanding. By 2014, the advantages of robots have become more apparent. This set of figures has become 56,000 yuan and 92,000 yuan. "Recruiting" robotic employees has secured strategic space for Highly. In Highly view, even in the cost of the Huangpu River, the compressor manufacturing industry can still be retained. "HR Part 2": Keeping track of the robot's archives How does the number of Haili's robots have reached? In mid-2015, IFR (International Federation of Robotics) counts the density of industrial robots in various countries of the world, with the highest number of 437 Taiwan/10,000 industrial workers, followed by Japan with 323 Taiwan/10,000 industrial workers, and the third with 282 units/ten thousand Germans. Industrial workers, while the world average of 66 Taiwan / ten thousand industrial workers, China only 36 Taiwan / ten thousand industrial workers, below the world average. Zheng Min stated that at present, the Shanghai factory has reached 569 sets/ten thousand industrial workers, and has surpassed the highest South Korea, and is at the world's leading level. In order to manage these robots well, the Shanghai factory has a “second human resources departmentâ€: the production technology department assumes the human resources management of the robots. More than 230 robots have invested a total of 187 million yuan in 2007, 288 jobs have been reduced, and 861 people ... Chen Jielu, chief of the automation promotion department, said that the production technology department will number each robot to keep track of the robot's return on investment. At present, one machine passes three shifts of working time, which is equivalent to the output of three production employees. According to the 2015 automation project calculation, the average investment return period is 3 years. On the other hand, the “second human resources department†is responsible for the “turning work†of the robot according to the adjustment of the work station, which can be easily realized by changing the manipulator configuration of the robot, reducing the difficulty of personnel transfer and labor costs, and has high versatility. The labor cost saved by the robot can also realize internal reinvestment. For example, after three years of depreciation to recover the investment, the labor cost saved by the robot continues to work and a pool of funds is formed to achieve self-recycling through reinvestment. Increased production capacity: The per capita production capacity increased from 295 to 1,131 units. Without robots, staff instability can cause production fluctuations. For example, departures and training of newcomers make staff operations fluctuate drastically, and human factors such as fatigue, worker's mood, and skill proficiency may also cause uncertainty. After the robots “go on dutyâ€, they can maintain a stable and efficient working status for a long period of time, achieve low production fluctuations, improve on-time delivery rates, reduce work-in-process inventory, and comprehensively improve on-site management. Compared with the efficiency of the robot, the efficiency of the robot is different at different time periods within a shift: the efficiency of the personnel is up to 90%, and the minimum is 0%. It will fluctuate at any time, and the efficiency of the robot will be stable at around 90%. Take the Shanghai factory sheet metal shell production line as an example. Before using the robot, there were 10 operators per class, with a production capacity of 2949 compressors, a per capita capacity of 295 units, and a per capita operating equipment of 1.2 units; after using robots, each class was reduced to 3 people. However, the production capacity was expanded to 3,392 units, with a per capita capacity of 1,131 units and 7.7 units of operating equipment per capita. Man-machine "dancing together": Workers' transformation is an inevitable move. Robots do not mean that workers are laid off. "In the year since the introduction of robots in 2007, there has been no centralized large-scale resignation." Zheng Min told reporters that there was a definite turnover rate for the first-line laborers. In addition to reducing recruitment, the replacement of nearly 1,000 workers by robots is a gradual decline. After the robot came, the "workers" who danced with it were also beneficiaries. “In 2005, we organized the Haili College of Power and jointly operated with the University of Television Broadcasting to allow workers to read college classes and undergraduate classes.†Zheng Min introduced that after training, some workers were liberated from the original heavy physical position and they are now on the spot. The work of the workers mainly focuses on equipment maintenance and product testing, and they are transformed into robot managers. Labor intensity declines and incomes increase substantially. The increase in income is the most visible "benefit." Highly use of robots in Highly, the increase in employee labor efficiency, the increase in employee income. Last year, the per capita annual cash income of the Shanghai factory sheet metal workshop rose from 37,000 yuan in 2007 to 84,000 yuan. In terms of improving occupational health, robots can replace artificial hands in harsh environments such as noise and high temperatures. According to reports, high-speed rushing station noise reaches 97 decibels, electric sawing saws wood sounds at 90 decibels, and exposure to noise from 70 decibels to 90 decibels for five years, the risk of hypertension is as high as 2.47 times. Workers who were originally engaged in high repetitiveness and labor intensity can work on jobs with higher skill requirements and lower labor intensity, which strengthens the company's ability to innovate and are more conducive to the realization of employees' personal values. It can be said that the use of robots is a win-win thing for both companies and employees. Highly Meaning: Robots Resolve Manpower Cost Pressures To upgrade and upgrade a company, it is not only necessary to develop new products, but also to require intelligent and flexible production. In the face of disappearing demographic dividends and high labor costs, the exploration of Haley's applied robots has sample significance for other companies. At present, the Highly Group has taken the lead in completing the international industrial layout in the industry. It has five world-class compressor plants and seven technical centers worldwide. Its products are sold in more than 160 countries and regions, and there are one for every seven air conditioners in the world. Hasli compressor is used. As a traditional household appliance manufacturing company, Highly was able to take the lead in realizing the internationalization of its industrial layout. One of the factors that has long dominated the world's top three market share is the introduction of intelligent automated production models and the introduction of robot “employees.†As robots can effectively resolve the pressure of rising labor costs and protect the advantages of domestic manufacturing companies in other areas, Zheng Min believes that China's status as a “world factory†will not be easily replaced. The world’s industrial robots have long been the most used in the automotive industry, working on welding, stamping and painting. But now, robots are "big attacks" in various industries, from the handling of valuables such as tobacco and Wuliangye, to the brick making, food and beverage industries, and even the feed industry. In fact, more and more labor-intensive companies in China have also begun to try robots. Zheng Min believes that Highly's robot application model is fully conditional in other batch, standardized, and process-oriented manufacturing industries. Highly is currently preparing a robot plan for 2020. In the future, most of the workshops in Shanghai are expected to be fully automated.
Diesel Generating Set,Genset Generator,Independent Power Supply,Office Buildings Generator
Shaoxing AnFu Energy Equipment Co.Ltd , https://www.sxanfu.com