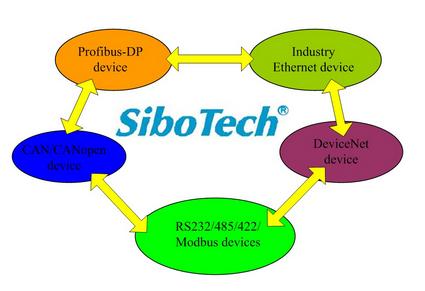
In the first 10 years of the new millennium, in the field of power automation, fieldbus has gone from concept to product, from pilot to promotion, from small-scale trials to large-scale applications. In this process, the controversy has never ceased. On the one hand, people are amazed at the new look that the fieldbus brings to the automation system. On the other hand, they are constantly tangling up with the new problems brought about by the fieldbus. As a practitioner in the field of power automation, the author has been observing this interesting phenomenon from a close distance and is thinking about it. He is trying to reveal the law behind the phenomenon from the essence of technology development and find the development direction of field bus technology to promote power automation. .
Dongfeng night spent thousands of trees, the field bus from concept to successful application in 10 years
If, from December 1999, the International Electrotechnical Commission voted through the IEC61158 fieldbus standard, it has been only 13 years since. The application of field bus technology in the field of domestic power automation, we have learned about also began in 1999. This year, Hangzhou Banshan Power Plant adopted the control system of Nanjing Keyuan Automation Group Company to carry out the automation transformation of two 135MW units. In order to shorten the project duration, when the project is designed, remote I/O is used to reduce the amount of cable construction, and the signal transmission with the DCS is realized through the field communication bus. The selected DCS has Profibus DPV0 communication interface and supporting remote I/O rack. In the control system of each unit, Profibus accesses 1417 I/O signals from 37 remote chassis installed on site. , accounting for 40% of the total system I/O points.
Strictly speaking, the Profibus application of the Hangzhou Banshan Power Plant is not a true fieldbus application, but it is only a serial communication protocol with high reliability and real-time performance for the industrial site, at the time of the domestic market. There is no intelligent device that supports fieldbus. It only transmits cyclic data such as process parameters. It does not support non-cyclic data such as diagnostic parameters. However, through the exploration of the Hangzhou Banshan Power Plant, the reliability and real-time performance of the field bus, especially Profibus, have been fully verified. The I/O cards and communication modules arranged in the remote chassis have been subjected to the on-site environment, especially the tests of temperature and electromagnetic interference, providing reference for real-world fieldbus applications.
In 2004, at Jiangyin Xiagang Power Plant, the infrastructure projects of two 300MW units selected 346 low-voltage motor protection units with fieldbus interfaces. Each motor protection unit exchanged data with the controller through the communication port of Profibus DPV1. The cyclic data for operation is transmitted, and acyclic data for diagnosis is also transmitted. In Guohua Ninghai closed circulating water system, the electric actuator is connected through Profibus; in Huaneng Yuhuan water treatment system, the transmitter, electric actuator and low voltage motor protection unit are connected through Profibus. During this period of time, with the emergence and maturity of intelligent devices that support fieldbuses, real-world fieldbus applications have grown from scratch and gradually evolved from small to large. Through this series of practices, fieldbus can reduce field cable construction and the advantages of providing rich diagnostic information are recognized. At the same time, the network structure and wiring scheme of the field bus and the intelligent devices supporting the field bus are gradually developed. However, the overall cost of the fieldbus system is high and the skill requirements of the maintenance personnel are also relatively high. The room for the user to select the fieldbus solution is very small, causing some problems.
In 2009, in order to pilot a digital power plant, two 1000MW ultra-supercritical units in Huaneng Jinling Power Plant were used for the largest fieldbus application in China. Its host control system and auxiliary control system have connected more than 1500 bus devices through Profibus, including low-voltage motor protection units, bus-type solenoid valve boxes, electric doors, regulating valves, pressure and differential pressure transmitters. Here, the field bus is no longer a supplement to the conventional control system, but it occupies 50% of all instrument control systems and becomes the main transmission method for controlling the system parameters. The reliability of the fieldbus has been fully verified to meet the control requirements of the largest single-capacity unit at that time. However, the diagnostic information provided by fieldbus intelligent devices lacks analytical management methods and tools and has not been effectively used. This problem and the higher cost of the fieldbus have caused a lot of obstacles.
The above three batches of typical fieldbus applications are separated by five years. The capacity of the single-machine application is getting larger and larger, and the range of applications is also wider and wider. The bus standards used are Profibus. As a brand-new technology in the field of industrial automation, the application of fieldbus in the domestic power industry has no apparent lag in the world, and it is basically a simultaneous development. Behind this development is the demand for new technologies for power automation brought about by the heavy industrialization of the Chinese economy. The market demand and advanced layout of power automation expert groups have become a powerful force for promoting the application of fieldbus technology in the domestic power industry in 10 years. In the time, the fieldbus has evolved from the concept of international standards to a completely new technology that has been successfully applied to the highest level of control systems in the power industry.
There is no doubt that there is no doubt about the heavy water, and the development of fieldbus is accompanied by continuous controversy.
Similar to the development of any new technology, the development of fieldbus is always accompanied by questions and controversies. The three representative questions are:
(1) The reliability of communications is low, and fieldbus cannot be used for critical applications;
(2) The real-time communication performance is not enough, and the field bus cannot be used for high-real-time control functions;
(3) The fieldbus connecting the control system and the field intelligent instrument are all invisible communication signals, so it is difficult for maintenance personnel to grasp and perform troubleshooting.
From the technical nature of the fieldbus, the above three problems are the twists and turns in the development and application of new technologies, and cannot be regarded as the defects of the fieldbus technology itself.
First of all, talk about the reliability of fieldbus. Before the fieldbus, the physical signals in the field were converted into electrical signals through sensors, and the standard electrical signals were sent to the I/O cards in the control system through hard-wired cables, processed into digital signals by A/D conversion, and finally entered the control. The system performs arithmetic processing. In the field bus system, the three links of D/A conversion, cable transmission, and control system A/D are simplified to direct communication between the on-site smart chip and the control system. Therefore, in principle, the reliability of the fieldbus is obviously better than the traditional hard wiring. Moreover, the fieldbus can transmit multi-point signals, and has a better price/performance ratio than hard wiring when performing redundant designs. At the same time, the diagnostic functions of the fieldbus can prevent signal failures more effectively and further improve the reliability of the entire control system. Therefore, from the point of view of technology, fieldbus has higher reliability. The question of reliability is more due to the maturity of fieldbus-related products. In particular, smart devices that support fieldbus are diverse and provided by different manufacturers.
Second, let's talk about the real-time nature of fieldbus. In the field of power automation process control, according to the control requirements, real-time performance is divided into two types: First, the collection and control of the general process signal requires the sampling period and control period to be more than 200ms to 500ms, covering more than 95% of the control requirements. The second is the acquisition and control of fast process signals. The sampling period and control period are required to be around 50ms, including special control loops such as FSSS, ETS and DEH. At present, fieldbus is mainly used for the collection and control of general process signals. For the adoption and control of fast process signals, traditional hard wiring schemes are still used. Analysis from the real-time performance of serial communication, for packets smaller than 64 bytes, with a baud rate of 500K, the transmission time is within 2ms. For the Profibus field bus with the highest baud rate of 12M, to meet the control cycle requirement of 50ms, there is no difficulty in the protocol itself. However, the overall design must be performed from the controller communication master station, the communication slave station of the on-site smart device, and the entire communication link, so as to meet the real-time requirements of the rapid process in a stable and reliable manner.
Finally, we will talk about field bus maintenance. From the technical point of view, the fieldbus standard and the 4-20mA electrical signal standard are used to standardize the signal exchange method between the control system and the field instrument. The 4-20mA electrical signal belongs to the technical knowledge of electrical engineering, and the fieldbus standard requires more knowledge of communication and software. It imposes higher requirements on maintenance personnel. However, fieldbus systems provide user-friendly debugging tools. In the case of establishing bus communication, the debugging efficiency for field instruments can be greatly improved. Therefore, the fieldbus makes higher demands on the maintenance personnel. This is not a technical defect, but is a requirement for updating the knowledge provided by the development of new technologies. Because field bus technology has not been promoted in the electric power industry, most power plant equipment and system maintenance personnel lack basic knowledge of field bus technology, and because the existing field bus in the power industry is mostly used in power plant auxiliary workshops, more To a large extent, it is just a test of a new technology, or simply a so-called bright spot in a large-scale infrastructure project. It has not been taken seriously by the management and the relevant technicians lack sufficient enthusiasm to master the necessary maintenance techniques.
From this point of view, from the technical point of view, reliability, real-time, and difficult-to-maintain controversy should not be obstacles to the development of fieldbus technology (current field bus application cases in the power industry have already demonstrated this). What are the obstacles that hinder the promotion and application of fieldbus? This is a question that the author has been pondering over.
Searching for thousands of Baidu in the public, affecting the obstacles of fieldbus promotion and application
To illustrate the issues raised above. We continue to analyze the nature of technology. The development of any new technology and the replacement of old technologies must be based on two prerequisites. The first is lower costs and the second is higher performance. Then:
First, is the cost after the application of fieldbus even lower? From the current point of view, after using the fieldbus system, the cost of the instrument control system has increased significantly.
Second, the cost can be improved to obtain higher performance? From the current application case, fieldbus provides a large number of diagnostic data, but the lack of analytical management methods and tools, has not been able to improve the power industry operating economic indicators Have a positive effect.
In this case, relying solely on the advanced layout of the power automation expert group, the fieldbus can only obtain a small number of pilot applications, but lacks market momentum for large-scale promotion.
At this point, there is a clear gap between the promotion and application of fieldbus in the petrochemical industry. According to the author's understanding, the power industry and the petrochemical industry are large-scale process industries. The controlled objects are complex and huge, and the physical dispersion is closely linked. Relatively speaking, the petrochemical industry has a greater degree of physical dispersion, and the equipment in the power industry is more concentrated. Therefore, the advantages of fieldbus in saving power cables and construction costs are less prominent in the power industry. The petrochemical industry also has explosion-proof requirements. If traditional hard wiring is used, a large number of safety barriers must be configured on the I/O interface of the control system. The cost of the safety barrier is equivalent to the cost of the entire control system. If an intrinsically safe fieldbus is used, I/O interfaces and corresponding safety barriers can be saved. For the petrochemical industry's control system, significant costs will be saved. Therefore, we believe that it is the overall cost disadvantage that has affected the promotion of fieldbus in the power industry.
In addition, it is also the reason for explosion protection. During the operation process, the petrochemical industry is not allowed to open the explosion-proof box to the site to perform field equipment maintenance. Instead, the field equipment must be debugged through a remote communication interface. The characteristics of the field bus exactly match the internal demand of the petrochemical industry and become a reason why the field bus is popularized and applied in the petrochemical industry. The same functional features have become an obstacle for maintenance personnel to adapt to it in the power industry.
In addition, the main advantage of fieldbus technology lies in providing diagnostic information of field devices, and providing data for power plant condition maintenance and fault diagnosis. In fact, due to the failure of fault diagnosis and equipment status overhaul in the domestic power industry, the large amount of equipment status information provided by fieldbus technology has lost practical significance. Power plants that have adopted fieldbus technology have not furthered these diagnostic information. The use of mining. This makes the fieldbus technology that should be widely used in the power industry always use "thunder and rain."
Liu Minghua Mingyin Village, adhere to the essence of the field bus era
Therefore, we believe that the essence of technology, the promotion of any new technology, its most powerful driving force can only come from the inherent needs of the market, that is: similar performance, lower cost; similar Cost, higher performance, best price/performance ratio.
According to such demand, the field bus must speed up the promotion and application in the power industry. The following are two major efforts:
The first is to reduce the overall cost of the user. The current high cost mainly comes from two aspects. One is that the price of smart devices supporting fieldbus is too high, and the other is that the price of fieldbus communication equipment is too high. We should not think that the high price of fieldbus equipment is a completely reasonable phenomenon. From the point of view of product manufacturing, the adoption of fieldbus will reduce the hardware cost of on-site smart devices. However, the cost of fieldbus communication equipment is not essentially different from the cost of common card components. The chip cost of fieldbus is not high. On industrial Ethernet chips. The cost of the development of new technology and new products is eliminated. The reason why the price of field bus-related equipment is too high is more of a monopoly in the market. Only more powerful domestic manufacturers are involved in the fieldbus field and achieve product performance similar to that of foreign competitors. Only by breaking the artificial technical barriers that cannot be interoperable between fieldbuses, even using industrial Ethernet to unify the fieldbus, only It may break this monopoly and provide the market with reasonably priced fieldbus products.
The second is to realize the analysis and management of diagnostic data of equipment, improve the efficiency of equipment management, and provide real value for saving energy and reducing consumption and reducing the overall operating cost of the power industry. This is more of an asset management function than a fieldbus system function. Fieldbus can provide a large amount of equipment diagnostic data for asset management, thereby improving the efficiency of asset management. In this respect, the Field Device Tool (FDT) has emerged in the fieldbus field. This is a development standard that integrates the intelligent field devices into the process automation system independently of the respective equipment manufacturers and fieldbus protocols. . FDT can send a large number of device diagnostic data to the asset management system in a standard way, so that the data advantages of the fieldbus can be brought into play, making the total site field truly become the basis of the digital power plant.
Conclusion
Adhering to the essential laws of technology and using innovative technologies to provide users with better and cheaper products is the king of market competition, and it is also the most powerful driving force for the development of field bus technology in the electric power industry. We believe that with the continued development of the Chinese economy and the advanced layout of experts, electric power automation will usher in a new era of fieldbus.
Bulkhead Lamp,Led Bulkhead Lamp,Round Bulkhead Light,Bulkhead Ceiling Light
Changxing Fanya Lighting Co.,Ltd , https://www.fyledlights.com