Guide: The servo system plays a crucial role in industrial automation and serves as the essential pathway to achieving precise positioning and motion control in the automation sector. Overcoming the key technological challenges within this system could significantly elevate China's technological prowess and market competitiveness in the realm of intelligent manufacturing.
China's Servo Market Size: In 2015, despite a sluggish overall economy and a slowdown in demand for servos in certain traditional manufacturing sectors, proactive national efforts to promote the robotics industry and "Industry 4.0" spurred market demand, particularly for network-type and bus-type servo systems. Despite these challenges, the servo market maintained robust growth in 2015. That year, the total market size reached 11 billion yuan. Looking ahead, with the continued development of the industrial robotics sector, the deeper penetration of industrial automation, and the progression of intelligent manufacturing, the servo market is poised for another wave of explosive growth. By 2020, the market is projected to expand to 25.4 billion yuan.
The trajectory of China’s servo market from 2015 to 2020 can be visualized below:
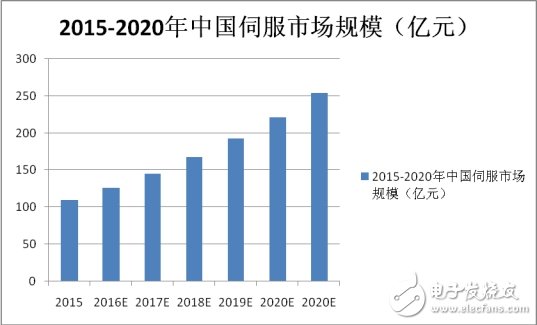
The servo system is built upon frequency conversion technology and functions as an automatic control system where mechanical position or angle serves as the control object. Beyond speed and torque control, the servo system offers precise, rapid, and stable position control.
The Working Mode of the Servo System:
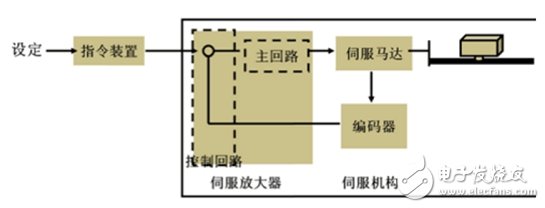
Currently, the most widely used electrical servo system consists of a servo drive and a servo motor, along with a servo feedback device (encoder). The servo drive falls under the drive layer in the automation control system, while the servo motor belongs to the execution layer. Both servo drives and motors are indispensable components of smart manufacturing.
The working process of the servo system can be simply explained as follows: The upper machine (PLC, control card) sends a pulse signal to the servo motor, and the upper machine governs the entire servo motion. The encoder serves as a feedback unit, verifying how many pulse signals the servo motor executes and feeding this information back to the drive for precise closed-loop control.
The servo motor encoder is a sensor located at the end of the servo motor to measure its angle and speed. Typically, it is integrated into the motor's end. Servo motor encoders, currently employed in the field of automatic control, include photoelectric encoders and magnetoelectric encoders. Photoelectric encoders determine the motor rotor's rotation angle through the number of light signals reflected by the photodisc, whereas magnetoelectric encoders detect the rotor's position by sensing magnetic field changes caused by the motor rotor's rotation via magnetic field induction components. The advancement of photoelectric encoders hinges on the precision of the code disc. Higher precision means more scale lines and a larger code disc size. The main technical challenge lies in processing the code disc. Magnetoelectric encoders use magnetic field induction components instead of a code disc, allowing for smaller volumes while maintaining high accuracy. Thus, magnetoelectric encoders are suitable for high-precision applications where space is limited. Although the magnetic field induction working principle is simpler and more reliable than the light reflection process, magnetoelectric encoders tend to be pricier. They are primarily used in high-precision fields and specific working conditions. As the price of magnetic field sensing components decreases in the future, magnetoelectric encoders may gradually replace photoelectric encoders.
As the signal feedback device of the servo system, the encoder significantly influences the system's accuracy. The servo drive powers the motor to run, the motor rotates with the encoder, and the feedback model from the encoder is sent to the controller. The controller can monitor the motor's operation, determining its speed, moving position, and distance. The controller calculates deviations based on signals fed back from the encoder, adjusts the motor's motion, corrects deviations, and precisely controls system variables like motor speed, position, distance, and torque.
Internal Structure of the Servo Encoder:
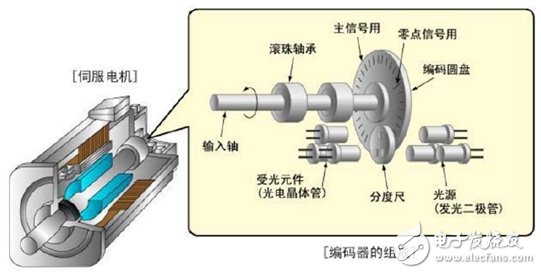
Encoder technology, one of the core technologies of the servo system, is highly challenging to develop high-precision encoders. Currently, most domestic and foreign servo systems rely on third-party encoders. Globally, the leading encoder company is Germany's Heidenhain, offering a broad product range and comprehensive offerings. Renowned companies like Japan's Nikon and Canon, leveraging their expertise in optical instrument production, have developed photoelectric encoders with stable performance, high precision, and long lifespans.
With increased domestic R&D investments, companies have begun mastering encoder technology. For instance, Huichuan Technology can now produce 23-bit encoders reaching international standards, thereby reducing the overall servo system's manufacturing costs and gaining a competitive edge.
This evolution underscores the growing maturity of China's servo system technology, positioning it as a pivotal player in global intelligent manufacturing.
The EI 35 Transformer is a specific model of low-frequency Power Transformer commonly used in various electronic applications, particularly in the realm of vacuum tube audio amplifiers (also known as valve amplifiers or "tube amps").
Basic Information
Model: EI 35
Type: Low-frequency power transformer
Structure: Features an EI-type core construction, comprised of two halves - an "E" and an "I" shape - made of laminated silicon steel sheets stacked together to form the magnetic circuit
Purpose: Primarily used for power conversion in electronic devices, particularly where stable voltage output is crucial, such as in vacuum tube audio amplifiers.
Technical Characteristics
High Efficiency: Designed for optimal energy conversion efficiency, minimizing energy waste.
Low Losses: Utilizes high-quality silicon steel sheets and refined winding techniques to reduce both core losses (hysteresis and eddy current losses) and copper losses, enhancing overall performance.
Excellent Thermal Management: The EI-type core structure promotes efficient heat dissipation, ensuring stable operation even under extended use.
Stable Output Voltage: Precisely wound and rigorously tested to deliver a consistent and stable output voltage, critical for maintaining audio fidelity in audio applications.
Applications
The EI 35 Transformer finds its niche in applications requiring reliable power conversion, notably in the audio industry. It serves as a cornerstone component in vacuum tube audio amplifiers, converting AC power into the DC voltages necessary to drive the amplifier circuitry, thus ensuring pure and stable sound reproduction.
Ei 35 Transformer,Low Voltage Transformer,35X15D Transformer,5kva transformer,Ei35 Transformer
Guang Er Zhong(Zhaoqing)Electronics Co., Ltd , https://www.geztransformer.com