1 Introduction
The seesaw system is a typical control system that is more complicated than the inverted pendulum system and is closer to practical application. It has the characteristics of severe nonlinearity, strong coupling, sensitivity to interference, and overly complicated models [2-5]. The seesaw system is composed of a cart, a DC servo motor, two potentiometers for measuring angle and position, and a seesaw triangle. The mechanism to balance the seesaw is to use the movement of the car in the seesaw system to complete the balance [6].
Due to the high nonlinearity and strong coupling characteristics of seesaw system and the chattering problem of variable structure control, this paper introduces fuzzy sliding mode control algorithm into the system control to soften the control amount. Using fuzzy control strategy can not only ensure and improve the quality of the sliding mode of the control system, but also eliminate the chattering phenomenon in the sliding mode control.
2 Mathematical model of seesaw system
The schematic diagram of the seesaw system is shown in Figure (1).
Figure (1) Schematic diagram of seesaw system
The parameters in the figure are defined as follows:
The tilt angle of the lever; X: position of the car; d1: height of the lever relative to the fulcrum 0.125m; d2: height of the lever center relative to the fulcrum 0.058m; Iw: moment of inertia 0.395kg.m2; mb: mass of the car 0.57ãŽ; mw: The mass of the lever is 3.6㎠;: Gravity acceleration is 9.81N / ãŽ.
Define Lagrange operator
L = TU (1)
Where T is the kinetic energy of the system and U is the potential energy of the system. Taking the state variable as, to construct the Lagrange equation, find out separately
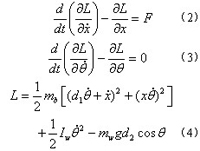
Substituting equation (4) into equations (2) and (3), we can get equations (5) and (6)
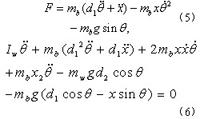
The expressions of sum can be obtained by (5) and (6) respectively
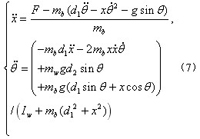
Equation group (7) is the expression of the nonlinear state equation of the system.
3 Design of fuzzy sliding mode controller
Sliding mode variable structure control has the advantages of fast response speed and strong robustness. It is widely used in nonlinear system control. However, sliding mode control is easy to cause chattering of the system, resulting in the ultimate instability of the system. Fuzzy sliding mode control is an intelligent control method for effectively controlling complex objects in uncertain environments. It does not depend on the model of the system, and is completely robust to interference, while maintaining the advantages of fuzzy control and sliding mode control. The basic design method of fuzzy sliding mode control is to compensate the influence of unmodeled dynamics by adjusting the control function of fuzzy logic during the approaching phase of the sliding mode control system. Its purpose is to improve the quality of the control system, reduce the time to reach the sliding surface, and reduce Chatter. In this paper, fuzzy control rules are used to adjust the size of the control input to ensure that the sliding mode control arrival conditions are met. The principle of fuzzy sliding mode control is shown in Figure 1.
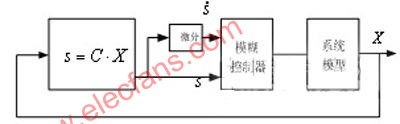
Figure 1 Schematic diagram of fuzzy sliding mode control
It can be seen from the figure that the fuzzy sliding mode control system consists of three parts, namely the switching function, the fuzzy controller, and the controlled object. The input of the sliding mode function is the system state variable, and the switching function is designed as s = C · X
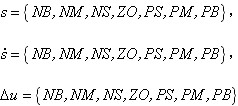
The input of the fuzzy controller is the switching function and its rate of change, which can effectively reduce the number of fuzzy rules and solve the problem of rule explosion in multi-input of high-order systems. As the output of the sliding mode controller, the amount of change in the control can make the fuzzy sliding mode control model-free and less dependent on the controlled object [7].
According to the principle of fuzzy control, define fuzzy sets,
Among them, PB, PM, PS, ZO, NS, NM, NB are expressed as positive, positive, positive small, zero, negative small, negative medium, negative large. Designed under the condition of satisfying the inequality, the obtained control table is shown in Table 1. The fuzzy rules used are
Table 1 Table of fuzzy control rules
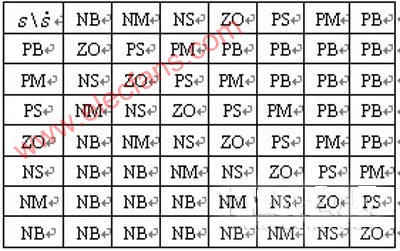
All the control rules in the table are designed based on satisfying the sufficient and necessary conditions to achieve sliding mode [8], so the designed fuzzy sliding mode control system is stable.
4 Simulation research

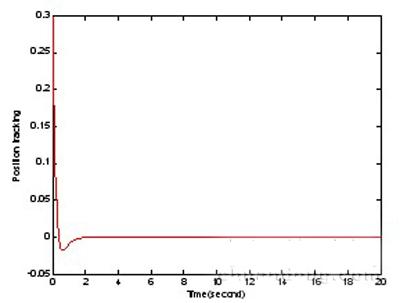
Figure 2 Curve of the position of the trolley with time
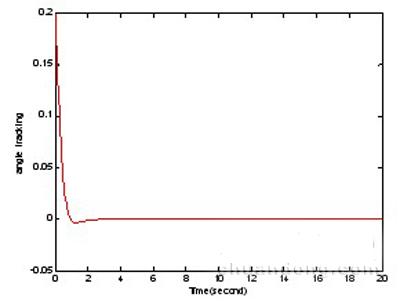
Figure 3 The curve of lever angle with time
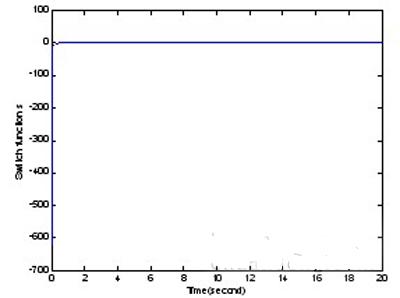
Figure 4 Change function versus time curve
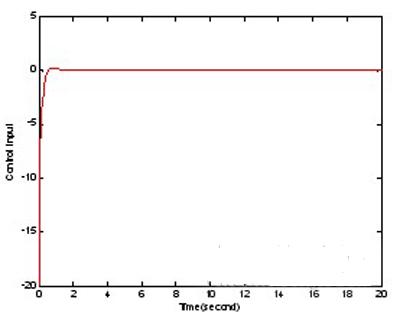
Fig. 5 Control law changes with time
It can be seen from the above simulation results that the controller designed by the scheme in this paper greatly accelerates the response speed of the system, and can effectively reduce the maximum deviation of the system, and the chattering phenomenon of the system can be basically eliminated.
5 Conclusion
This paper introduces the working principle of the seesaw system and establishes the mathematical model of the seesaw system. Aiming at the chattering phenomenon in the conventional sliding mode control, the fuzzy sliding mode control method is introduced into the seesaw control system. It can be seen from the simulation that it is feasible to apply the fuzzy sliding mode control to the seesaw system with strong coupling and nonlinear characteristics , And the controller designed by using sliding mode fuzzy control algorithm is very robust.
Dongguan Andu Electronic Co., Ltd. , https://www.idofuseholder.com